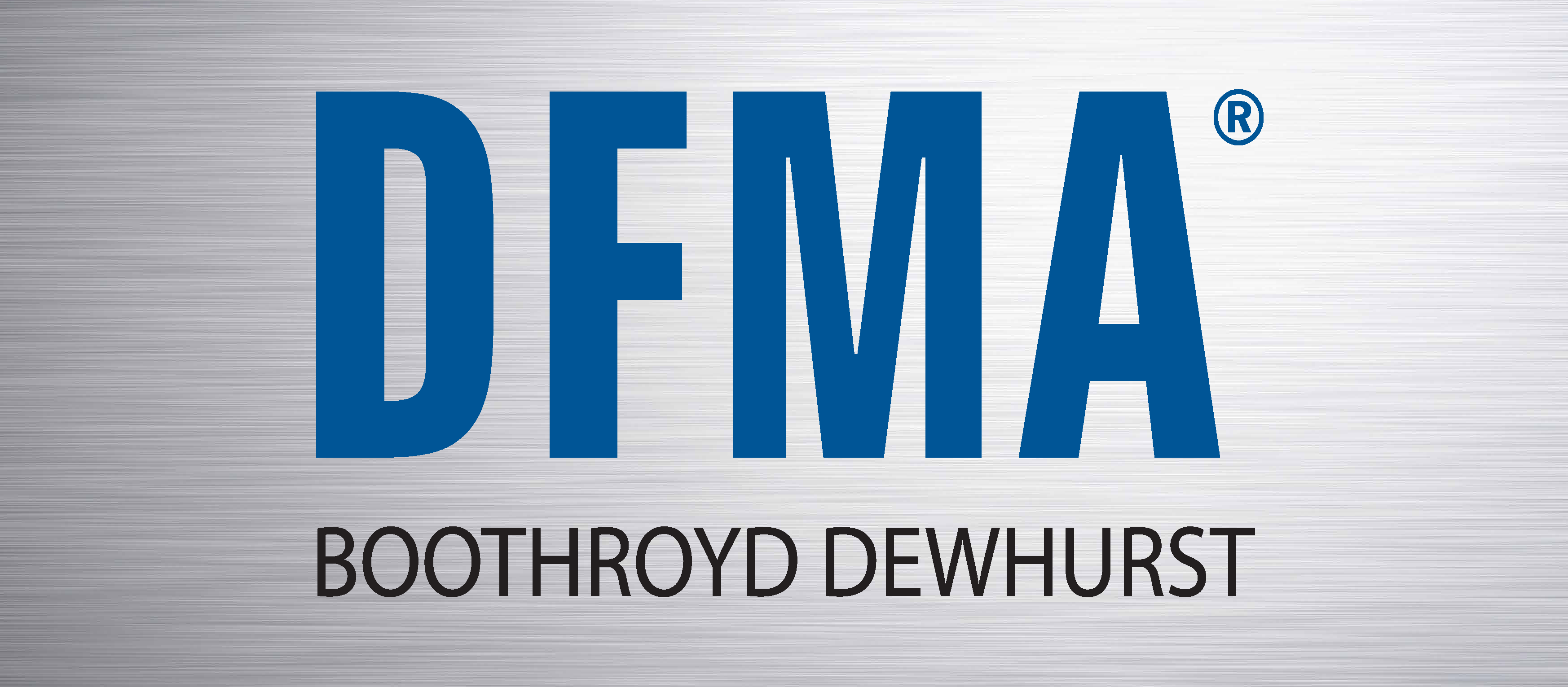
DFMA®: Now More Than Ever
To produce world-class products domestically, with shorter, more efficient supply chains, at lower costs, companies must:
- Make product designs as efficient as possible by minimizing their part count.
- Completely understand the cost to manufacture the parts that make up each product design.
Outsourcing in order to reduce cost has been perceived as a best practice for some time now. COVID-19 has turned the manufacturing world upside down and there is much to consider as we begin our return to “normal.” Undoubtedly, as a result of the pandemic, global supply chains will shrink. Organizations are already rethinking the true cost of outsourcing to low-cost labor regions. The average customer has likely faced financial challenges and, as a result, is even more interested in price reductions, so pressure to keep costs low will remain. The companies that will be most successful reshoring their products for domestic production won’t do so by increasing prices to the customer. This puts manufacturers in a predicament: build products domestically and at a lower cost. But how?
Fortunately, the solution has been here all along – proper evaluation of the product design itself. And two things can be done right now to ensure success. First and foremost, make the product design as efficient as possible by using multi-function parts to reduce the part count. Secondly, completely understand all part manufacturing should-costs for each and every part in the product design. Achieving these two objectives has been proven, over time, to unlock substantial savings that many have thought not possible. Better yet, the downstream impact of a reduced part count means quicker time to market, shorter domestic supply chains, inherent increases in quality and reliability, and shortening (yes shortening!) of design cycles.
Product Design:
Product development teams with the foresight to design cost out of their products will come out on top with the customer as we overcome the impact of COVID-19. Thinking now about products in development, while also re-thinking the supply chains that will produce them, is crucial. This becomes especially important for products originally slated to be manufactured overseas because the efficiency of those designs is most consequential. Design for Manufacture and Assembly (DFMA) enables a systematic, objective, big picture look at a product and guides development teams towards the most efficient use of parts in their designs. And efficient use of parts in a product design has been proven the key to a substantially reduced manufacturing cost.
The savings shown below represent typical averages achieved when companies used DFMA on a wide sample of mechanical and electro-mechanical products.
Top ten responses quoted from over 170 case studies | |
42% | |
54% | |
57% | |
22% | |
60% | |
45% | |
73% | |
53% | |
45% | |
50% |
When a candidate for re-shoring is already in production overseas, it’s even more important to ensure that parts are used most efficiently in its design. This is because a product with fewer parts and a simplified structure is much more likely to be manufactured cost effectively using a primarily domestic supply chain. In some cases, the use of DFMA has enabled manufacturers to supply their customers with a domestically produced product while still delivering a reduction in cost. But in every case, DFMA tilts the balance in your favor during re-shoring projects and greatly increases your chances of success.
Understanding true manufacturing cost:
Today, as companies overwhelmingly work with a global supply chain centered around the Asia-Pacific region, much of the understanding and detail surrounding manufacturing cost has been lost. Management of these lengthy and complex supply chains was difficult before the pandemic, but now it’s practically impossible. Important decisions, with far-reaching consequences, are commonly made using a seat-of-the-pants approach, like choosing from a series of competing price quotes. A much more fruitful and efficient strategy is to base decisions on the foundation of an independent DFMA analysis that identifies the most important drivers of manufacturing cost. Communication, understanding, and teamwork are all improved because the DFMA results are based on the “science” of the manufacturing process and are delivered in terms of time and cost, a language that everyone can easily understand. The most successful organizations drive discussions with their suppliers based on independent estimates of the true manufacturing should-cost, instead of arguing about price.
DFMA is an independent true cost analysis
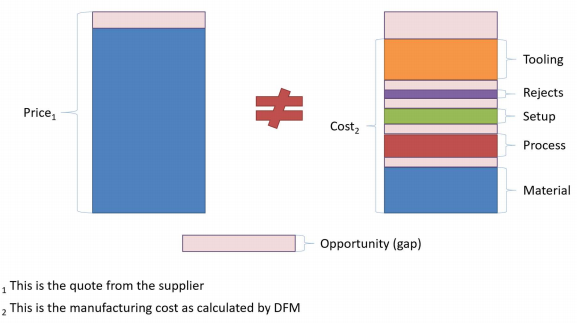
Several problems occur when supplier negotiations are carried out without the availability of true manufacturing costs. As illustrated on the left above, with this approach there is generally a complete lack of visibility into the price charged by the supplier. This leaves most organizations flat-footed and with no option except to establish cost reduction goals based on arbitrary price reduction demands made to the supplier. These arbitrary price reductions often leave money on the table because they are not based on an understanding of the true manufacturing costs involved. They can also weaken the supply chain and risk putting price competitive suppliers out of business, which is bad for everyone. A much more productive and fair approach is to base supplier negotiations on an independent DFMA estimate of the true manufacturing costs, as shown above on the right. The discussions that take place during this process should have the objective of understanding the individual differences between the DFMA estimates of material, process, setup, rejects, and tooling costs and the corresponding prices charged by the suppler. DFMA identifies all major cost drivers for each step of the manufacturing process so that the important cost related questions can be asked during these discussions. This exposes additional opportunities for savings, which are completely missed when the true manufacturing costs are not fully understood. A win-win collaboration with your suppliers results when these talks are based on DFMA estimates of the true manufacturing cost.
For more than 30 years, Boothroyd Dewhurst has helped companies achieve significant savings in cost at every stage of product development. We have the time-tested and proven software tools, techniques, and resources to help you and your company achieve its cost reduction goals. Get in touch with us today so we can show you how.
About Boothroyd Dewhurst, Inc.
Boothroyd Dewhurst, Inc. was the first company to commercialize Design for Manufacture and Assembly (DFMA®) methodologies and software tools, which make it possible to evaluate, estimate, and reduce the manufacturing cost of a product in the design phase through product simplification and cost estimation. Hundreds of Fortune 1000 companies, including General Electric, John Deere, Motorola, Pratt & Whitney, and Dynisco, use DFMA® to cut the costs of their manufactured products and achieve design innovation in their markets. The company was founded in 1983 and received a National Medal of Technology Award in 1991. For more information about DFMA® software, workshops, consulting services, and international conferences, contact Boothroyd Dewhurst, Inc., 138 Main Street, Wakefield, RI 02879, USA. Tel. (401) 783-5840. Fax (401) 783-6872. Web site: www.dfma.com. E-mail: info@dfma.com.
DFMA® is a registered trademark of Boothroyd Dewhurst, Inc.